What Woods Are Best for Carving? A Complete Guide for Beginners and Experts
Discover the Perfect Wood Types to Transform Your Carving Projects from Ordinary to Extraordinary
Are you pulling your hair out trying to pick the right wood for your next carving project? I’ve been there too. When I first started carving, I wasted money on wood that splintered or fought me every step of the way. Truth is, whether you’re just starting out or you’ve been carving for years, choosing the right wood makes all the difference between a frustrating experience and a rewarding one.
Basswood and butternut consistently rank as top choices among carvers for good reason – they’re soft, forgiving, and hold detail beautifully. But they’re just the beginning of your options. From the fragrant cedar to the rich, darkening cherry, each wood type brings its own personality to your carving.
In this guide, I’ll walk you through everything I’ve learned about carving woods over my 15 years of working with them. We’ll cover the soft, forgiving woods perfect for beginners, and the challenging hardwoods that experienced carvers can’t get enough of. By the time you finish reading, you’ll know exactly which wood to grab for your next project, ensuring your creative vision comes to life just as you imagined it.
Â
Introduction To Wood Carving
Wood carving is one of those ancient crafts that never seems to go out of style. There’s something magical about transforming a plain chunk of wood into something beautiful. It definitely demands patience, steady hands, and a creative eye.
I’ve seen wood carving serve as both a relaxing weekend hobby and a serious profession. Some folks I know have dedicated decades to mastering this craft. Let’s take a quick journey through the rich history and modern approaches to wood carving.
History Of Wood Carving
Wood carving runs deep in human history. Our ancestors were carving wood for tools, shelters, and art long before written language existed. They made do with whatever sharp objects they could find – usually stones or bones.
The ancient Egyptians took wood carving to a whole new level. Their craftsmen created incredibly detailed statues, elaborate furniture, and decorative items. Many of these pieces depicted their gods, pharaohs, and animals with surprising accuracy.
During the Middle Ages, European wood carving really hit its stride. If you’ve ever walked into an old cathedral, you’ve probably seen the stunning wooden altars, panels, and figures. This period gave us those distinctive Gothic and Renaissance styles that still influence carvers today.
In Asia, wood carving developed its own unique traditions. Chinese and Japanese artisans became famous for their elegant furniture, ceremonial masks, and religious figures. Their work often showcases patterns and details so intricate they seem almost impossible to create by hand.
Modern Wood Carving
Today, wood carving remains popular worldwide. Modern carvers use everything from traditional hand tools to power equipment, depending on their preference and the project at hand.
Wood carving generally falls into a few main categories:
- Whittling: This is the simplest form, often done with just a pocket knife while sitting on the porch.
- Relief Carving: Here, you create raised designs on flat surfaces – think of those decorative wooden panels.
- Chip Carving: This technique involves removing small chips of wood to create patterns.
- Caricature Carving: This style produces those exaggerated, often humorous figures that make people smile.
Today’s carvers work with various woods – basswood, butternut, oak, and others. Each type brings its own personality and challenges to the table.
Modern technology has also found its way into wood carving. CNC machines and laser cutters can now create precise designs quickly. But there’s still nothing quite like the character and warmth of hand-carved pieces. That’s why traditional methods remain popular despite technological advances.
Wood carving communities, both in-person clubs and online forums, have become important resources for sharing techniques and inspiration. Whether you’re just starting out or have been carving for decades, these networks offer valuable support and knowledge.
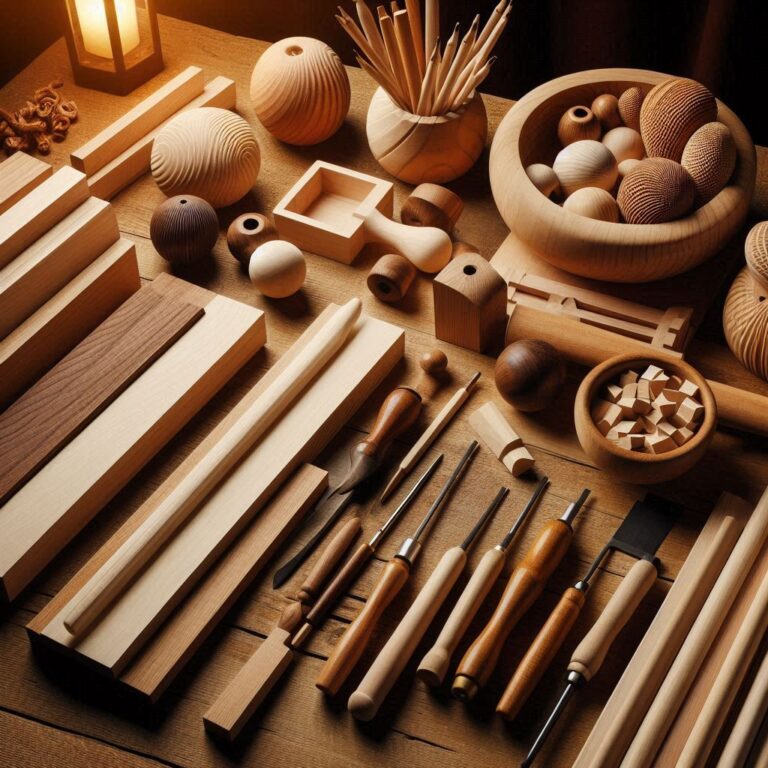
Essential Tools For Wood Carving
After 15 years of carving, I’ve learned that having the right tools makes all the difference. Good tools aren’t just about making the job easier – they can transform your entire carving experience. Let’s talk about what you’ll need to get started and then what you might want to add as you progress.
Basic Tools
When I first started carving, I wish someone had told me exactly what I needed instead of wasting money on fancy tools I wasn’t ready for. Here’s what every beginner should start with:
- Carving Knives: You’ll need a good general-purpose knife for shaping and cutting. I started with a simple Mora knife and still use it today.
- Gouges: These curved tools come in various shapes and sizes. They’re perfect for scooping out wood and creating curves. A U-shaped gouge (#5 or #7 sweep) is a great starter.
- Chisels: Nothing beats a chisel for straight cuts and fine details. A 1/4 inch and 1/2 inch will handle most beginner projects.
- Mallet: A wooden mallet lets you tap chisels through harder wood without damaging your tools. Avoid metal hammers – they’ll destroy your chisel handles.
- Sharpening Stone: Dull tools are dangerous tools. A basic combination stone (1000/6000 grit) will keep your edges sharp.
Advanced Tools
Once you’ve got the basics down, you might want to expand your toolkit. These aren’t necessary for beginners, but they can really elevate your work:
- Veiners: These specialized gouges create fine lines and details, perfect for things like leaf veins or hair textures.
- V-tools: My personal favorite for creating sharp, angular cuts and deep grooves. They’re invaluable for outlining and texturing.
- Fishtail Gouges: These have a flared shape that lets you reach into tight corners. I use them constantly for tight spots.
- Micro-Carving Tools: For those tiny details that make a piece stand out. They’re definitely a luxury, but worth it for miniature work.
- Power Carving Tools: From rotary tools like Dremel to specialized power carvers, these can speed up rough shaping dramatically.
Choosing The Right Wood
I’ve learned through plenty of trial and error that choosing the right wood can make or break your project. Different woods have unique personalities – some are cooperative, others fight you every step of the way. Understanding these differences will save you headaches and help you match the right wood to your project.
Softwoods
Softwoods come from coniferous trees and generally have more forgiving fibers. They’re my go-to recommendation for beginners because they’re easier on both your tools and your patience:
- Pine: Dirt cheap and available everywhere. Pine has a decent grain pattern but can be a bit unpredictable with its soft and hard spots. I use it for practice pieces and rough drafts.
- Cedar: Smells amazing while you work it. Cedar is lightweight and naturally resistant to rot, making it great for outdoor projects. The reddish color adds warmth to carvings.
- Redwood: Super soft and takes detail surprisingly well. Redwood is perfect for delicate projects where you need to carve thin sections without breaking.
Hardwoods
Hardwoods come from deciduous trees and require more skill and sharper tools. The trade-off is durability and often more beautiful grain patterns:
- Oak: Tough as nails but rewarding. Oak has distinctive grain patterns that can add character to your piece. I reserve it for projects that need to stand up to wear and tear.
- Maple: Dense and smooth, maple takes fine detail beautifully. It’s hard work to carve but polishes to a gorgeous finish. Worth the effort for showcase pieces.
- Cherry: My personal favorite for its workability and color. Cherry starts pale but darkens to a rich reddish-brown over time. It’s a perfect middle ground between soft and hard woods.
Type of Wood |
Characteristics |
Best For |
Pine |
Soft, knots common |
Practice, rough drafts |
Cedar |
Light, fragrant, rot-resistant |
Outdoor projects |
Redwood |
Soft, even texture |
Detailed small carvings |
Oak |
Strong, pronounced grain |
Durable pieces, furniture |
Maple |
Hard, smooth |
Fine detail work, heirloom pieces |
Cherry |
Medium hardness, ages beautifully |
All-purpose, display pieces |
Popular Wood Types For Carving
Over the years, I’ve worked with dozens of wood types. Some I’ll never touch again, others I keep coming back to. Let me share my experiences with the most popular carving woods.
Basswood
Basswood is the undisputed champion for carvers, especially beginners. There’s a reason you’ll find it in almost every carving shop:
- Soft enough that you won’t wear yourself out
- Has a fine, even texture that doesn’t fight your tools
- Holds detail remarkably well – I’ve carved feathers so fine they look like they might float away
- Perfect for learning techniques without frustration
- You can find it in almost any craft store, often pre-cut in carving blanks
My first successful carving was a small owl made from basswood. Despite my beginner skills, the wood was so forgiving that the piece turned out surprisingly well. It remains my go-to recommendation for anyone starting out.
Butternut
Butternut has earned a special place in my workshop. It offers a perfect balance of qualities:
- Light and relatively soft, making it easy on your hands during long carving sessions
- Features a beautiful grain pattern that adds character to your finished piece
- Takes detail well without being as bland as basswood
- Has a natural warm, honey color that deepens with age
- Less prone to splitting than many other woods, forgiving minor mistakes
I once carved a series of wildlife figures from butternut for a local art show. The wood’s natural color variations added dimension to the animals without needing additional staining.
Oak
Oak is not for the faint of heart, but it offers rewards for those willing to tackle it:
Characteristic |
Description |
Hardness |
Very hard – keep your tools extra sharp |
Grain |
Pronounced, adding natural texture |
Durability |
Exceptionally durable, will last generations |
Best Uses |
Furniture accents, outdoor pieces, items that need to withstand handling |
Challenges |
Can be difficult to carve against the grain, requires patience |
I reserve oak for special projects that need to stand up to heavy use. My carved oak coat hooks have survived 12 years of winter coats being thrown at them – something a softer wood would never tolerate.

Cherry
Cherry wood offers a perfect middle ground that experienced carvers often graduate to:
- Rich color that starts pale but darkens to a beautiful reddish-brown
- Grain patterns that add subtle interest without overwhelming your design
- Medium hardness that’s challenging but not exhausting
- Ages beautifully, developing deeper character over time
- Takes a polish like no other wood, creating a natural glow
My cherry wood serving spoons have developed a deep, rich patina over years of use. The wood seems to improve with age – something I appreciate as a carver who wants my pieces to last.
Preparing Wood For Carving
Proper preparation can make even difficult woods more cooperative. I’ve ruined enough projects by rushing this step to know it’s worth taking the time to get it right.
Drying Wood
Working with properly dried wood is non-negotiable if you want your carving to last. Green (freshly cut) wood contains moisture that will eventually cause warping, cracking, or splitting as it dries. Here’s how I handle drying:
- Air Drying: The traditional method. I stack wood with small spacers between pieces in my shed. It takes patience – about one year per inch of thickness – but results in stable wood.
- Kiln Drying: When I need wood faster, I’ll buy kiln-dried stock. Commercial kilns carefully control temperature and humidity to speed up the process without damaging the wood.
- Microwave Drying: For small pieces, I’ve had success using a microwave. I heat the wood for 30 seconds, let it cool completely, then repeat until it stops losing weight.
I always check moisture content with an inexpensive moisture meter before carving. You’re looking for 6-8% moisture content for most indoor projects.
Cutting And Shaping
Getting the basic shape right before detailed carving saves time and frustration:
- Choose the Right Tools: I use a bandsaw for initial cuts, but a good handsaw works too. Avoid splintering by using sharp tools.
- Mark Your Design: I draw directly on the wood or transfer a pattern using carbon paper. Good planning prevents major mistakes.
- Remove Excess Wood: Take off the largest chunks first. No sense in carving away material you could have cut off.
- Rough Out the Shape: Get the basic form established before moving to detail work.
I learned the hard way to take my time with this step. Nothing’s more frustrating than spending hours on detailed carving only to realize your proportions were off from the beginning.
Drying Method |
Time Required |
Best For |
Air Drying |
Several months to years |
Large pieces, no rush |
Kiln Drying |
A few weeks |
Medium to large pieces, when time matters |
Microwave Drying |
Minutes to hours |
Small projects, quick results |
Basic Carving Techniques
Getting comfortable with basic techniques will build your confidence before tackling more complex projects. I spent my first year just practicing these fundamentals.
Whittling
Whittling is where most of us start – it requires minimal tools and can be done almost anywhere. I still enjoy whittling on my porch in the evenings:
- Start with a soft wood like basswood or pine – my first whittling project was a simple pine bear that looked more like a potato, but we all start somewhere!
- Hold the knife in your dominant hand, with your thumb against the back of the blade for control.
- Always cut away from yourself – I have the scars to prove why this matters.
- Make small, controlled cuts rather than trying to remove too much at once.
The push cut (pushing the blade away from you with your thumb) and pull cut (pulling the blade toward you with controlled pressure) are foundation skills worth mastering. My whittling improved dramatically once I got comfortable with these basic cuts.
Relief Carving
Relief carving creates the illusion of three dimensions on a flat surface. It’s more complex than whittling but incredibly rewarding:
- Choose a hardwood like oak or maple for durability – my first relief carving was a maple leaf in maple wood.
- Transfer your design to the wood using carbon paper or by drawing directly on the surface.
- Establish the deepest parts first, creating different levels or “relief” in the wood.
- Work from the highest points to the lowest, gradually adding detail.
Sharp tools are absolutely essential for relief carving. I resharpen my gouges frequently during a project – dull tools tear the wood rather than cutting cleanly.
Both techniques require practice more than anything else. My early attempts were pretty rough, but each project taught me something new. The satisfaction of creating something from a block of wood keeps me coming back to carving year after year.
Advanced Carving Techniques
After mastering the basics, you might want to explore more challenging techniques. These approaches require more skill and patience, but the results can be truly spectacular.
Chip Carving
Chip carving has become one of my favorite techniques for creating geometric patterns and designs. It’s meditative and precise:
- The technique involves removing small “chips” of wood with careful knife cuts.
- I primarily use a specialized chip carving knife with a thin, sharp blade.
- Basswood works beautifully for chip carving – its consistent grain doesn’t fight you.
- Following the grain direction is crucial – I mark grain direction before starting.
Tool |
Usage |
Chip Knife |
Making precise triangular or rectangular cuts |
Stab Knife |
Creating starting points and tight corners |
Chisel |
Cleaning up areas between chips |
My kitchen is full of chip-carved wooden spoons and utensils. The technique adds beautiful texture without interfering with function.
Sculptural Carving
Sculptural carving is where wood truly becomes art. Creating three-dimensional figures requires planning and patience:
- Start with a clear vision – I usually make a clay model first for complex pieces.
- Choose wood with appropriate grain direction for strength – a face looks different carved with vertical versus horizontal grain.
- Remove large areas first with gouges and mallets – I wasted years trying to do everything with small tools.
- Gradually refine the form with smaller tools, working from general to specific.
- Sand selectively – sometimes tool marks add character and shouldn’t be removed.
My sculptural pieces take weeks or months rather than days. My first attempt at a human figure looked more like a melting snowman, but each project improves your understanding of form and proportion.
Both chip carving and sculptural work build on basic techniques but require a deeper understanding of wood properties and tool handling. The satisfaction of creating something truly unique makes the learning curve worthwhile.
Finishing Touches
The finishing process transforms a good carving into a great one. I’ve seen beautiful carvings ruined by poor finishing, and mediocre ones elevated by careful attention to these final steps.
Sanding And Polishing
Sanding prepares the surface for finishing and can highlight the beauty of the wood grain:
- Start with coarse sandpaper (80 grit) to remove tool marks and rough spots.
- Work through progressively finer grits – I typically use 80, 120, 180, and 220 for most projects.
- Always sand with the grain, not against it – cross-grain sanding leaves scratches that become visible under finish.
- After sanding, I raise the grain by lightly dampening the wood with water, letting it dry, then sanding once more with the finest grit.
For special projects, I’ll polish after sanding using super-fine steel wool or even burnishing with a smooth stone. This creates a surface that almost glows before applying any finish.
Sandpaper Grit |
Purpose |
80 |
Removing tool marks and shaping |
120 |
Smoothing the surface |
180 |
Fine smoothing |
220 |
Preparing for finishing |
Applying Finishes
The right finish protects your work and enhances the wood’s natural beauty:
Oils penetrate the wood and bring out its natural color and grain. Linseed oil was my first finish and remains one of my favorites for its warm, natural look. Tung oil offers better water resistance and a slightly harder finish.
Waxes create a soft, touchable surface that’s easily refreshed. I love beeswax for small handled pieces like wooden spoons – it’s food-safe and develops a beautiful patina with use.
Varnishes provide the most protection but can look plastic if over-applied. I use them sparingly, and often thin the first coat to allow better penetration.
- Before applying any finish, ensure the wood is clean and dust-free.
- Apply thin coats – building up thin layers always works better than one thick coat.
- Allow proper drying time between coats – rushing this step ruins the finish.
- For most projects, I sand lightly between coats with 320 or 400 grit paper.
My favorite finish for display pieces is a hand-rubbed oil/varnish blend. It offers the best of both worlds – the depth of oil with the protection of varnish.
Caring For Carved Wood
Proper care ensures your wooden creations last for generations. Some of my earliest carvings still look beautiful thanks to regular maintenance.
Cleaning
Regular cleaning prevents dust and grime from building up in the crevices of your carving:
- For routine cleaning, I use a soft brush to remove dust – old makeup brushes work perfectly.
- For stubborn dirt, slightly dampen a soft cloth with water and mild soap.
- Never soak wood carvings – water is the enemy of wood.
- Dry immediately and thoroughly after any cleaning that involves moisture.
I keep my carvings away from direct sunlight and heat sources. Sunlight fades wood over time, and heat can cause cracking as the wood dries out.
Repairing Damage
Even with careful handling, accidents happen. Here’s how I address common issues:
- For small scratches in finished pieces: • Rub the scratch with a walnut or pecan nut – the natural oils often make minor scratches disappear. • For deeper scratches, touch up with a matching colored wax stick before re-waxing.
- For more serious damage: • Clean the damaged area thoroughly. • Apply wood filler that matches your wood type. • Once dry, sand carefully to blend with the surrounding area. • Refinish the repaired section, feathering the edges to blend with the original finish.
For cherished pieces with significant damage, consider consulting a professional restorer. Some repairs require specialized knowledge and tools.
Frequently Asked Questions
What Is The Best Wood For Carving?
From my experience, basswood takes the crown for all-around carving excellence. It’s incredibly cooperative under your tools, holds fine details without crumbling, and forgives minor mistakes better than any other wood I’ve tried. The fine, even grain means you can carve in any direction without fighting the wood.
When I teach beginners, I always start them with basswood. You can find it in almost any craft store, and it’s affordable enough for practice pieces. Butternut runs a close second if you want something with a bit more character and warmer color.
How To Choose Wood For Carving?
I choose wood based on three main factors: the project type, my skill level, and the desired final appearance.
For intricate detail work, I grab basswood or butternut without hesitation. Their fine grain and consistent texture make detail work a joy rather than a struggle. For larger outdoor projects, I’ll opt for cedar or oak despite the additional effort required to carve them.
Always examine the piece before buying. I look for straight grain, minimal knots, and no visible cracks. A good trick is to tap the wood – a solid, resonant sound usually indicates wood without internal defects.
Is Hardwood Good For Carving?
Hardwoods like oak and maple are challenging but rewarding for certain projects. I’ve carved plenty of hardwood pieces, but I wouldn’t recommend them for beginners or for projects requiring fine detail.
The main advantages of hardwoods are durability and beautiful grain patterns. My oak carvings have survived years of handling and use. Hardwoods also take a polish beautifully, developing a rich patina over time that softwoods can’t match.
The downside? You’ll need extremely sharp tools, more physical strength, and a good dose of patience. You’ll also need to work more gradually, taking smaller cuts to avoid splitting the wood.
Should I Use Green Or Dry Wood?
After years of experimenting with both, I firmly believe dry wood is best for most carving projects. Green wood might seem easier to cut initially, but the headaches begin as it dries and potentially warps or cracks.
That said, certain traditional techniques like spoon carving actually benefit from green wood’s pliability. If you do use green wood, design your project with the inevitable shrinkage and movement in mind.
Most of my early green wood projects developed splits as they dried. Now I stick to properly dried wood (6-8% moisture content) for anything I want to last.
Conclusion
Finding the right wood for your carving projects makes all the difference between frustration and satisfaction. Each type of wood has its own personality and purpose. After years of trial and error, I’ve found that matching the wood to both the project and your skill level is the secret to success.
Don’t be afraid to experiment with different woods as your skills grow. The basswood that serves you well as a beginner might feel limiting once you’re ready for more challenging grains and textures. The journey of discovering each wood’s unique qualities is part of the joy of carving.
Remember that practice matters more than perfect materials. Even with the ideal wood, carving takes patience and persistence. But with each project, your hands learn the language of the wood, and your tools become extensions of your creativity. Happy carving!